

Human Machine Interface (HMI)
It is referred to as the Operator Interface Terminal (OIT) or Man Machine Interface (MMI) or Graphical User Interface (GUI) or Member Interface (MI), is the Interface between Machine (controller) and Human (operator).
01
HMI Controllers are used by
Operators
Managers
Supervisors
02
In Industrial settings, HMIs can be used to
Visual Display data
Track Production time, trends and tags
Oversee KPIs
Monitor machine inputs and outputs
Dignose and Debug
03
Industries using HMI Include
Fresh water maker
Food and Beverages
Chemical Manufacturing
Oil and Gas
Liquid Processing
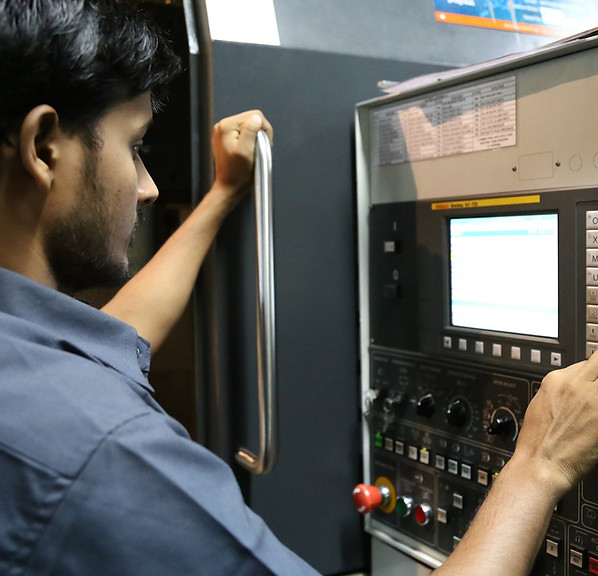
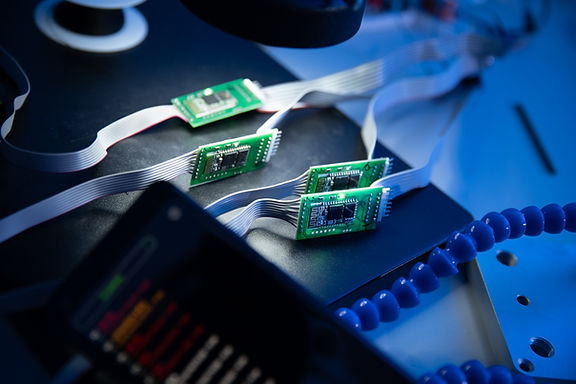
Cloud Based HMI Controllers
​
-
Device based configurations from Server.
-
Live monitoring of all units and it's status on the IoT platform's dashboard.
-
Over-the-air (OTA) screen and funtional updates.
-
Installations and remote diagnosis via BLE from Mobile devices.
HMI IoT
Web based UI Tool + Display + Processor + 4G LTE Gateway
-
Web based UI tool or browser based UI utility
-
7 inch touchscreen display 800 x 480 resolution
-
Processor Cortex-A53 64-bit for IoT and HMI applications
-
Embedded Linux OS based event driven IoT model
-
Multiple options to connect with PLCs and Automation Controllers
-
Wireless 4G LTE fall back 2G, BLE communication
-
Tracking via GPS and triangulation
-
Role based access and authentication
-
IoT platform for device management, health monitoring
-
OTA for screen and firmware update & parameters config
-
OS and Firmware version management
-
Issue and ticket management for change request (CR)

Embedded UI Tool + Display + Processor + 4G LTE Gateway
-
Embbeded UI tool or local UI utility, can run on any computer
-
4.3 inch touchscreen display 480 x 272 resolution
-
Processor Cortex-A7 32-bit for IoT and HMI applications
-
Embedded RTOS based event driven IoT model
-
Multiple options to connect with PLCs and Automation Controllers
-
Wireless 4G LTE fall back 2G, BLE communication
-
Tracking via GPS and triangulation
-
Role based access and authentication
-
IoT platform for device management, health monitoring
-
OTA for screen and firmware update & parameters config
-
OS and Firmware version management
-
Issue and ticket management for change request (CR)
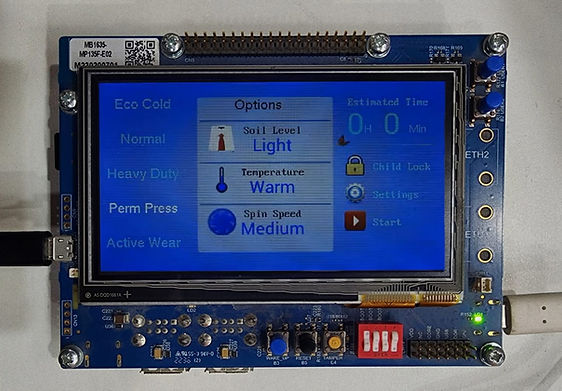
Automation Controller
Programmable Automation Controller (PAC) + Expansion IO
-
Micro-controller ARM M7 600MHz
-
1MB internal RAM, 4MB flash and external SD card storage
-
Connection with HMI and Communication boards
-
USB, isolated CAN, isolated 485 and ethernet
-
Onboard IOs: 16 digital in, 16 digital out, 16 analog in, 2 analog out and 2 encoder
-
External IO Board: 16 Digital I/O, 16 Analog Input and 4 Analog Output communicate with IAC with RS 232, RS485 and CAN protocol.
-
External Communication: Wired - RS-232, CAN, Ethernet, RS485, USB and Wireless - MQTT/ HTTP, GSM, BT.
-
Isolated power supply
-
RTC with on board battery, Buzzer and LEDs for indication
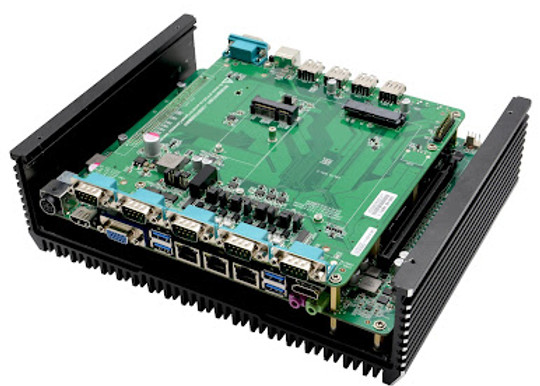
IoT enabled Automation Controller (IAC) with Independant HMI
Experience The Unlimited Power of IoT with Inditronics
01.
Unlimited read-write clients
02.
Unlimited Tags
03.
Modern UI/ UX
04.
IO Communication drivers
(wired and wireless)
05.
Cloud and Mobile App Integration
Full Control Panel Manufacturer
-
HMI Display - inditronics and other manufacturer
-
IoT enabled Automation Controller (IAC), Programmable Automation Controller (PAC) and Programmable Logic Controller (PLC)​
-
Power Supply (multi in & out and fixed)
-
Drivers and Control Circuits
-
Dual Low Side Driver - Rectifier
-
Four channel Power Switch
-
Operational Amplifier
-
-
I/O Cards
-
Analog input and analog output
-
Digital input and digital output
-
-
Internal Panel
-
Switches, Contact breakers, MCB, Relays, Terminal strip
-
-
Cabinet
-
Enclosure, Glands, Wires
-
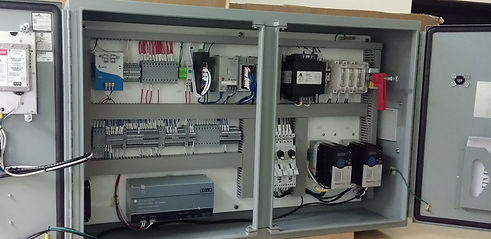
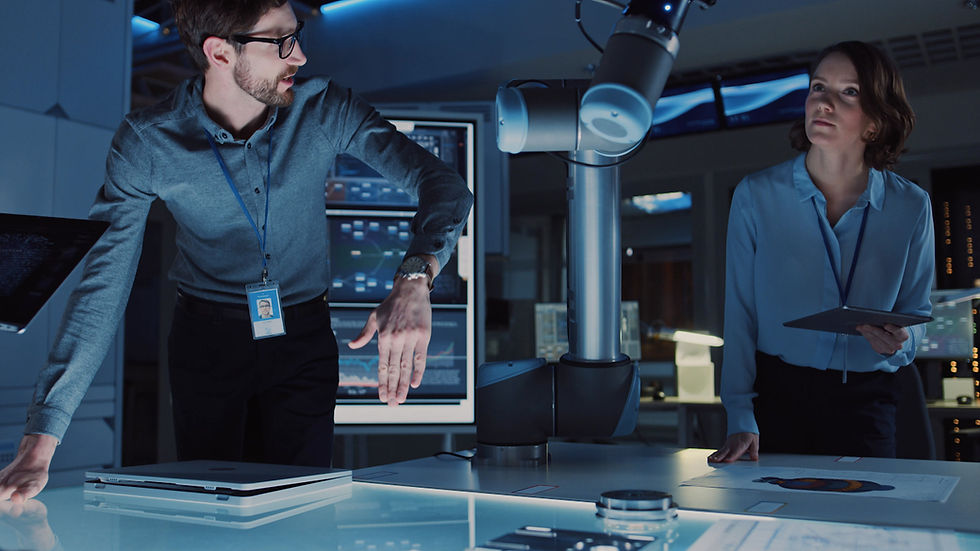
AI Powered
IoT enabled Automation Controller
Automated Statistical Process Control (SPC) using Machine Learning
Custom
Custom rule creation, dynamic and continuous data acquisition
Faster
Faster response for corrective measures against limit breaches
Automated
Tracking & Alert when parameters out of control limites
Case Study: HMI IoT Automation Controller for Reverse Osmosis (RO) Water Maker
01. Opportunuity Improvement Areas
TURNAROUND TIME
-
Extended time for change, resulting in downtime.
-
Monopoly Interface Software limits system control.
-
There are no Monopoly Interface Software options for hardware.
-
Vendor dependency due to proprietary systems.
UNIT COST
-
PLC design is complex.
-
Unwanted peripherals in the PLC.
-
Complex brand change.
-
Not ideal for IoT.​
FLEXIBILITY
-
Reasons determined by the manufacturer.
-
Obsolete hardware and parts.
-
No wireless or SPC upgrades.
-
Not ideal for IoT.
02. Hardware Architecture
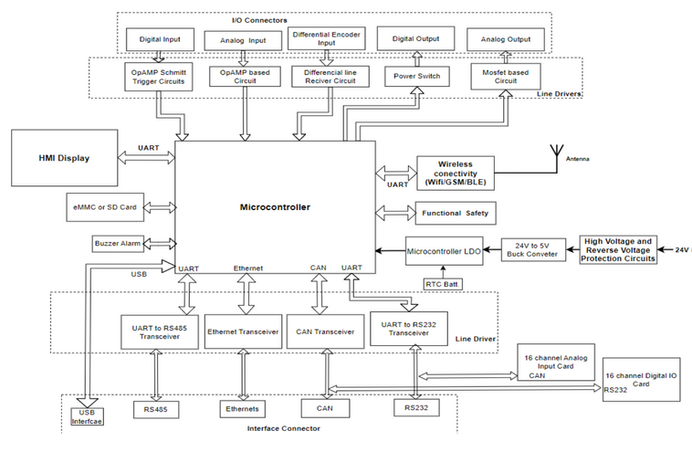
Approach is to design a system which will be easy to develop, maintain and use in the field and also to be feature rich and scalable for further enhancements.
-
The IoT enabled Controller combine an operator (OT) interface (7” or 10”), logic controller, IoT communication capabilities, and local communication in a single unit.
-
The simplicity of programming the HMI maintained via HMI designer studio.
-
The PLC programming replaced by embedded C programming to write the control logic of the system.
-
IoT and remote (M2M) communication protocols, functions implemented via a separate communications co-processor.
-
The co-processor independently implement functions like data transfer, cloud communication and OTA etc.
-
Local communication protocols implemented via the peripherals internal and external to the microcontroller.
03. RTOS Based IoT Edge Application
Event-Driven Model:
The system follow an event-driven model, where events from sensors, user inputs, and external devices trigger specific actions and processes.
Benefits of this model:
-
Loosely coupled time scheduled task
-
OTA update ability
-
Device level security
-
Remote Diagnostics
-
Multiple connectivity options
-
Data encoding

04. Key Specifications




05. Benchmarking
